Expert Tips on Streamlining Operations for QC Businesses
Understanding the Importance of Streamlining Operations
In today's competitive market, quality control (QC) businesses face the challenge of maintaining high standards while optimizing their processes. Streamlining operations is not just about cutting costs; it's about enhancing efficiency and delivering superior quality products or services. By focusing on operational excellence, QC businesses can improve their reputation, increase customer satisfaction, and ultimately drive profitability.
Streamlining operations involves analyzing current workflows, identifying bottlenecks, and implementing strategies to improve them. It requires a combination of technology, human resources, and strategic planning. Here are some expert tips to help QC businesses streamline their operations effectively.
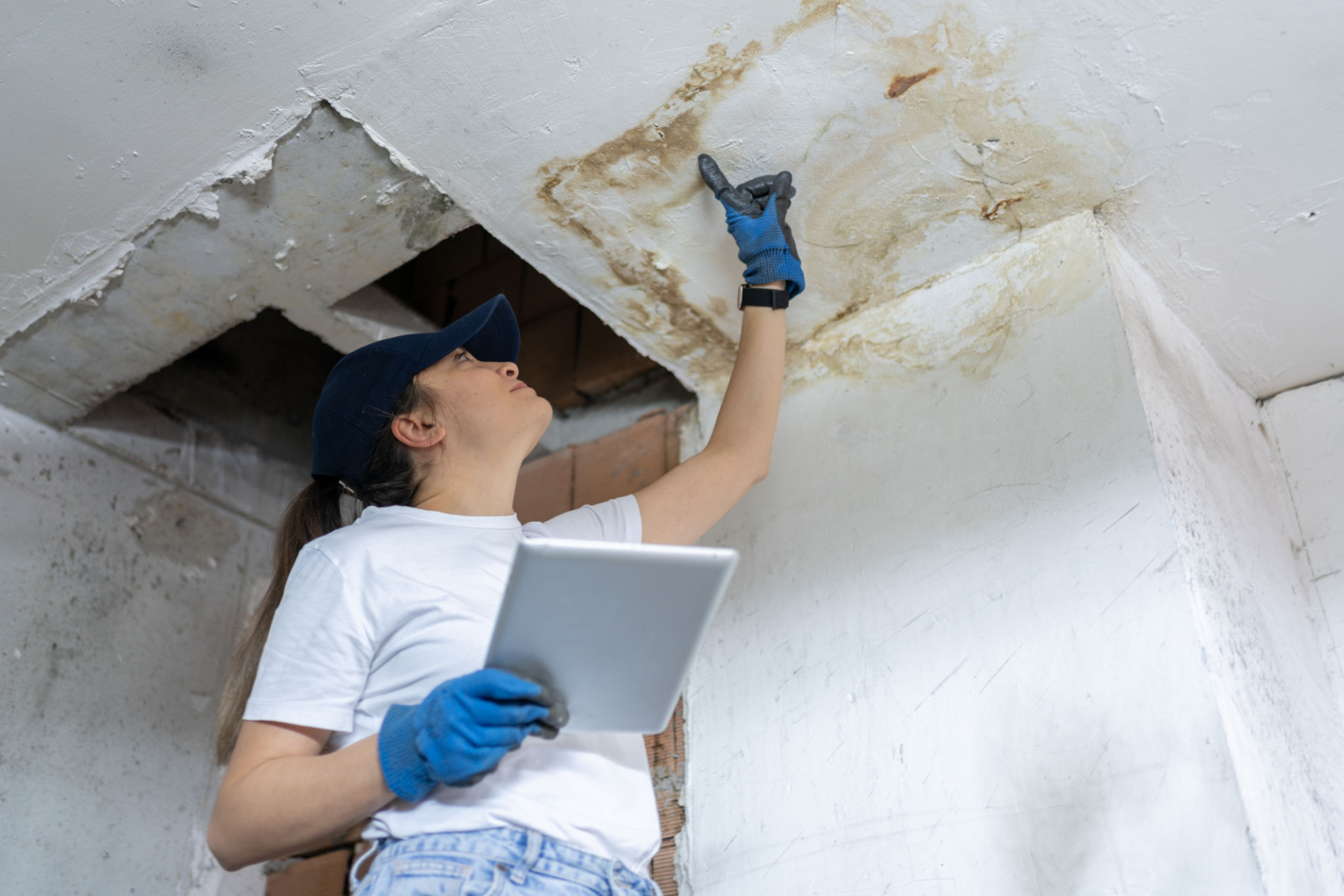
Implementing Advanced Technology
Leveraging advanced technology is crucial for QC businesses looking to streamline their processes. Automation tools can significantly reduce manual tasks, allowing employees to focus on more strategic initiatives. For instance, integrating AI-driven software can enhance data analysis capabilities, leading to more accurate quality assessments and faster decision-making.
Another technological advancement is the use of real-time monitoring systems. These systems provide instant feedback on production processes, enabling QC teams to identify issues promptly. By adopting these technologies, businesses can minimize errors and reduce downtime, resulting in a smoother operation.
Embracing Digital Transformation
Digital transformation is not just a buzzword; it's a necessity for modern QC businesses. By digitizing records and using cloud-based solutions, companies can enhance collaboration and ensure data accessibility from anywhere. This shift not only streamlines communication but also aids in maintaining consistent quality standards across different locations.
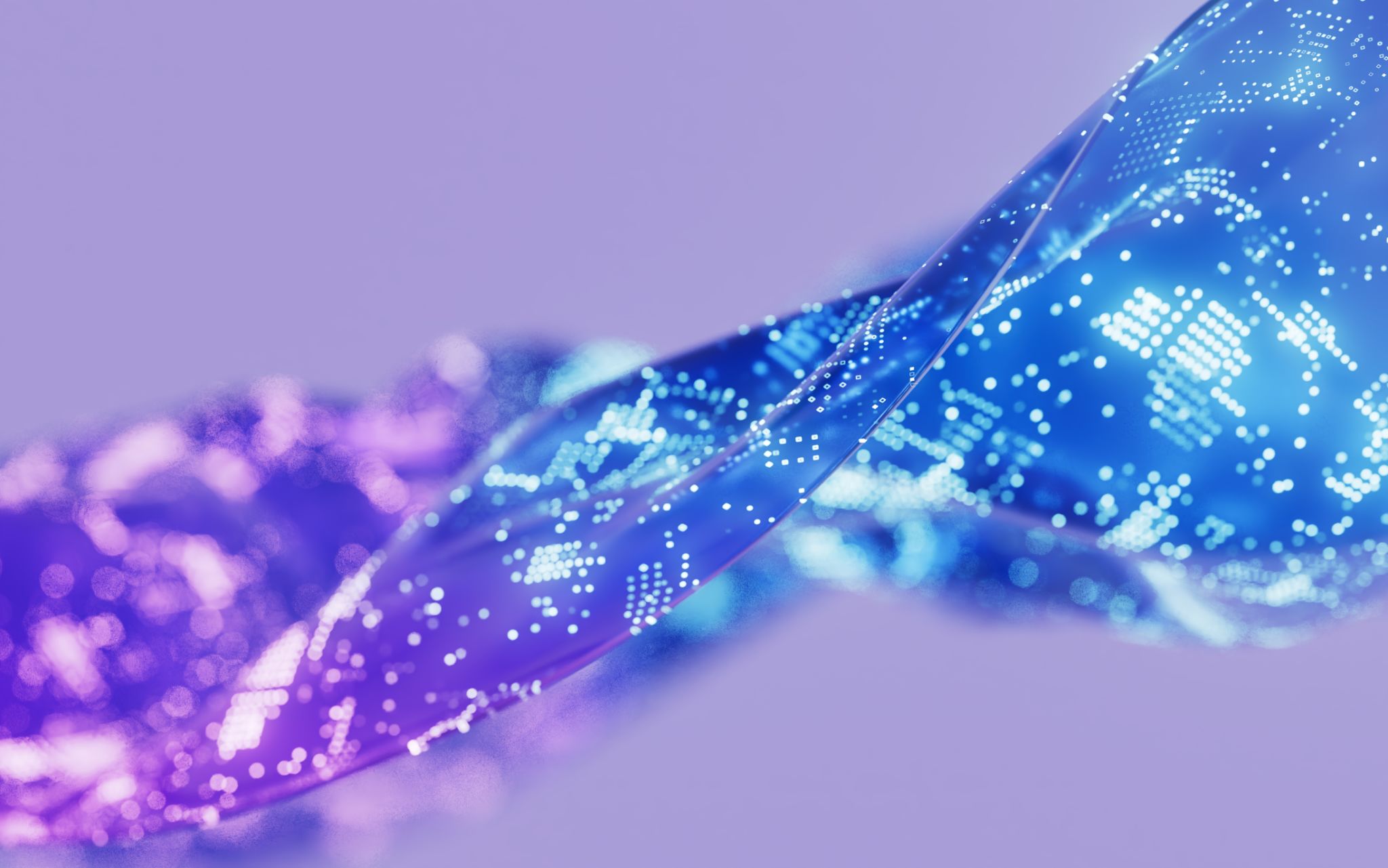
Optimizing Workforce Efficiency
A well-trained and motivated workforce is vital for streamlined operations. QC businesses should invest in regular training programs to keep employees updated with the latest industry trends and technologies. Encouraging continuous learning can lead to innovative solutions and improved operational efficiency.
Moreover, fostering a culture of teamwork and open communication can significantly impact productivity. Empowering employees to share ideas and feedback can lead to process improvements that might otherwise be overlooked. Recognizing and rewarding employee contributions further boosts morale and engagement.
Strategic Resource Allocation
Effective resource allocation is fundamental in streamlining operations. QC businesses need to prioritize tasks based on their impact on quality and efficiency. This involves assessing current resource utilization and redistributing them where they are most needed.
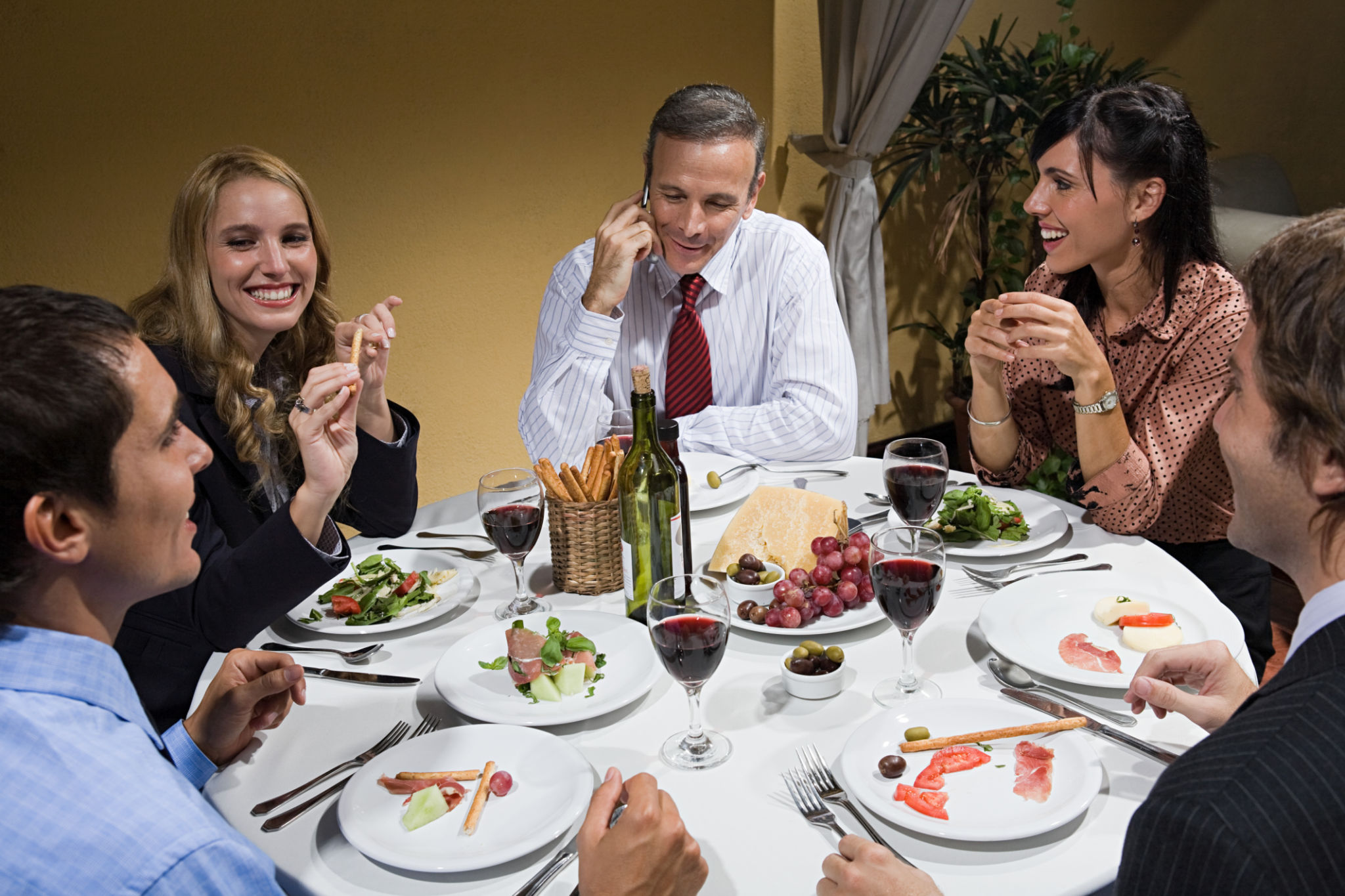
Continuous Improvement and Feedback Loops
The journey towards streamlined operations is ongoing. Implementing continuous improvement methodologies, such as Six Sigma or Lean, can help QC businesses identify areas for improvement and implement changes systematically. These methodologies focus on reducing waste, improving process flow, and ensuring consistent quality output.
Establishing feedback loops is also essential for sustained improvement. Regularly reviewing performance metrics and soliciting feedback from customers and employees can provide valuable insights into operational strengths and weaknesses. This information can guide future strategies and help maintain a competitive edge.
Conclusion: The Path Forward
Streamlining operations in QC businesses requires a strategic approach that combines technology, workforce optimization, and continuous improvement. By embracing these expert tips, companies can enhance their operational efficiency, improve quality outcomes, and achieve long-term success in the industry.