Top Strategies to Improve Business Operations in QC
Understanding the Importance of Quality Control
Quality Control (QC) is an essential aspect of any business operation, directly impacting customer satisfaction and operational efficiency. It involves the systematic processes of ensuring that products and services meet established standards and specifications. Implementing robust QC strategies can significantly enhance the overall performance of a business.
Businesses in Quebec City, known for their diverse industries, can benefit immensely from improved QC practices. Whether you're in manufacturing, retail, or service delivery, optimizing QC is crucial for maintaining competitive advantage and driving growth.
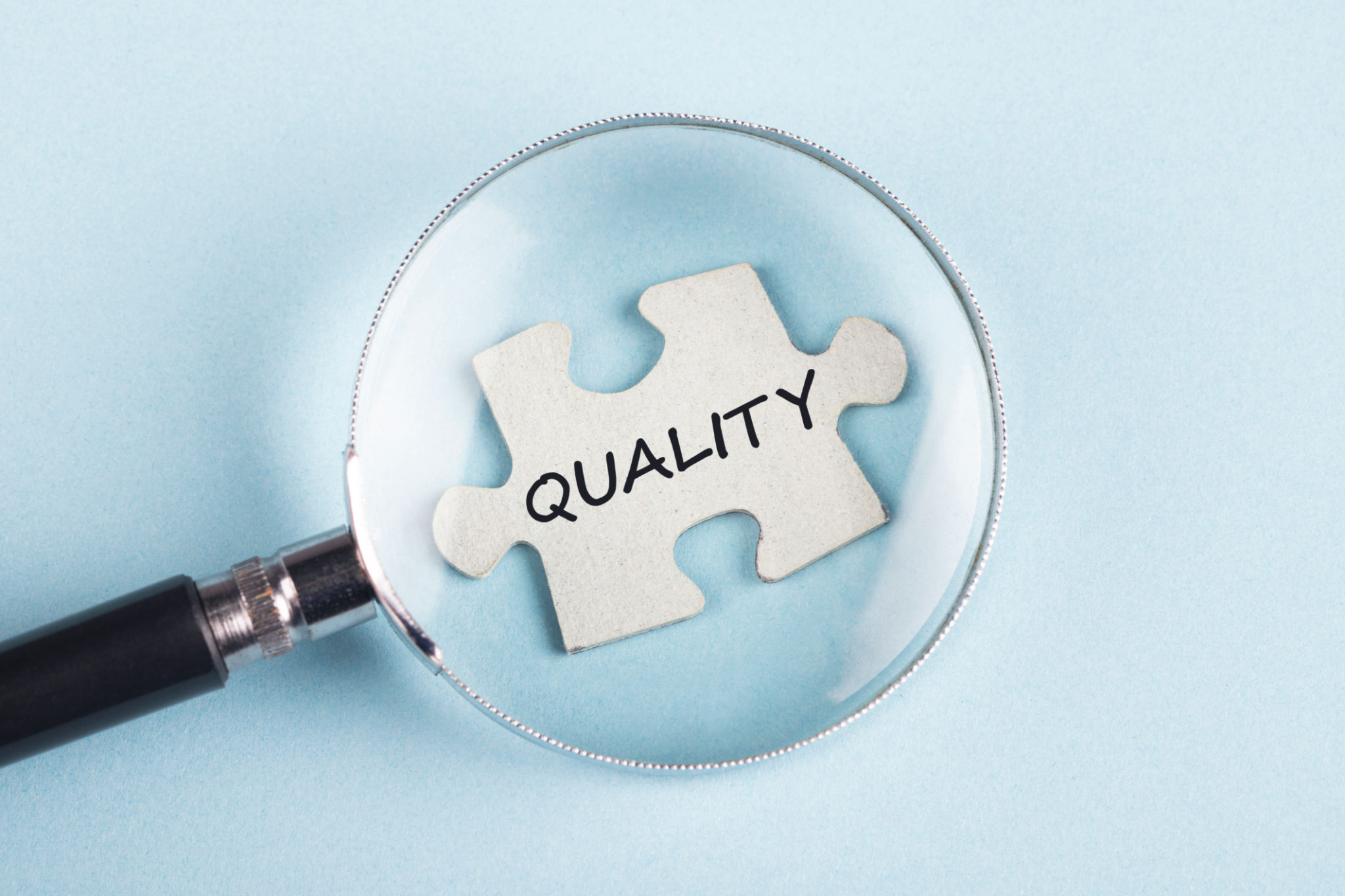
Adopting Technological Advancements
Incorporating technology into QC operations can streamline processes and reduce human error. Automated systems, such as AI-driven inspection tools and IoT-enabled devices, provide real-time data analysis and monitoring. This technology can identify defects and inconsistencies quicker than traditional methods.
Additionally, implementing cloud-based solutions for data storage and management facilitates seamless access to QC data across various departments. This integration enhances communication and ensures that everyone is aligned with the quality objectives.
Benefits of Automation
Automation in QC not only improves accuracy but also increases efficiency. By reducing manual interventions, companies can save time and resources, allowing employees to focus on more strategic tasks. Moreover, automation ensures consistency in product quality, which is vital for maintaining customer trust.
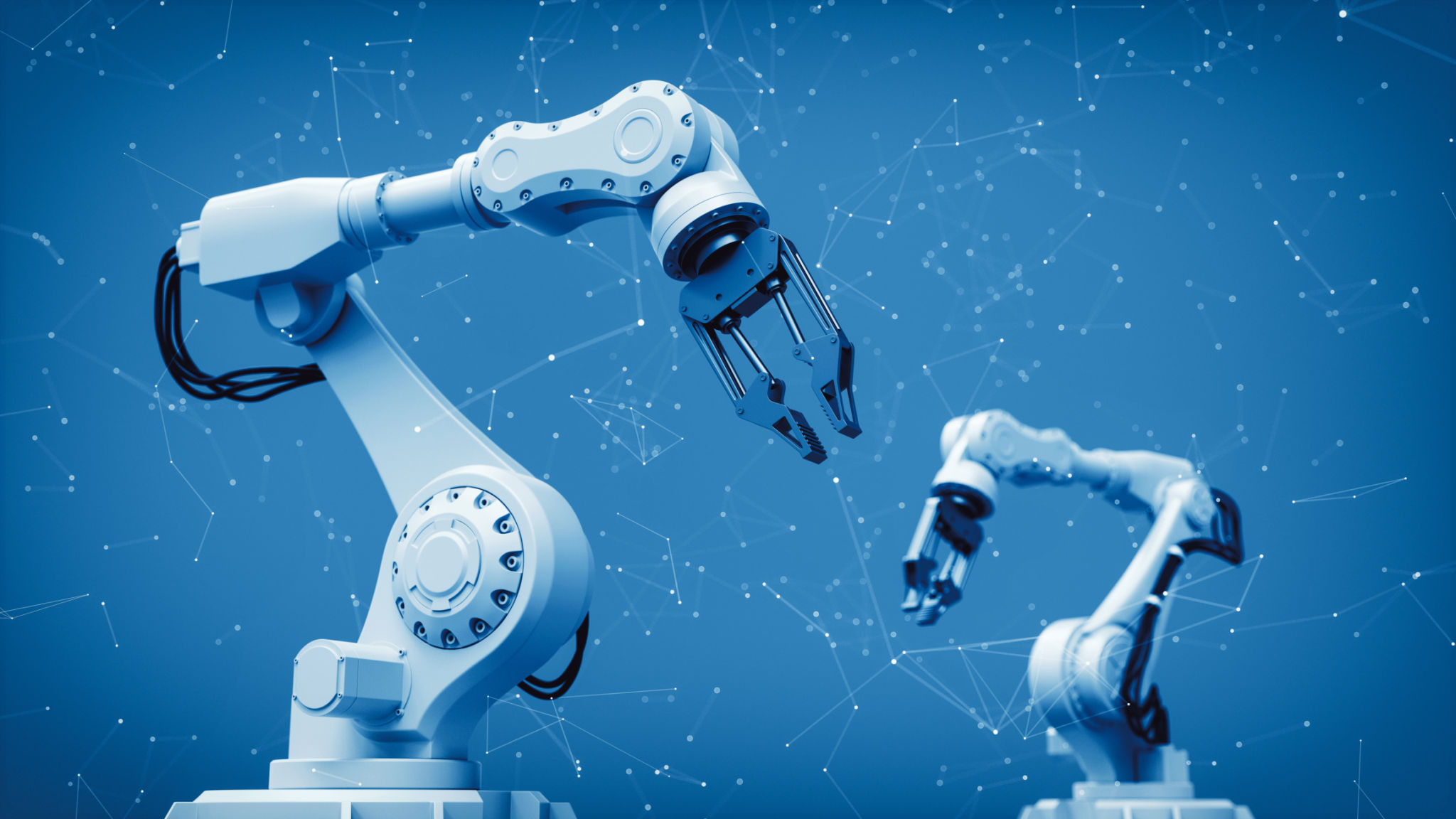
Implementing Continuous Training Programs
Employee training is a cornerstone of successful QC strategies. Regular training programs ensure that staff members are up-to-date with the latest QC techniques and technologies. This knowledge empowers them to identify potential issues early and take corrective actions promptly.
Investing in continuous education also fosters a culture of quality within the organization. Employees who understand the importance of QC are more likely to take ownership of their roles and contribute to overall operational excellence.
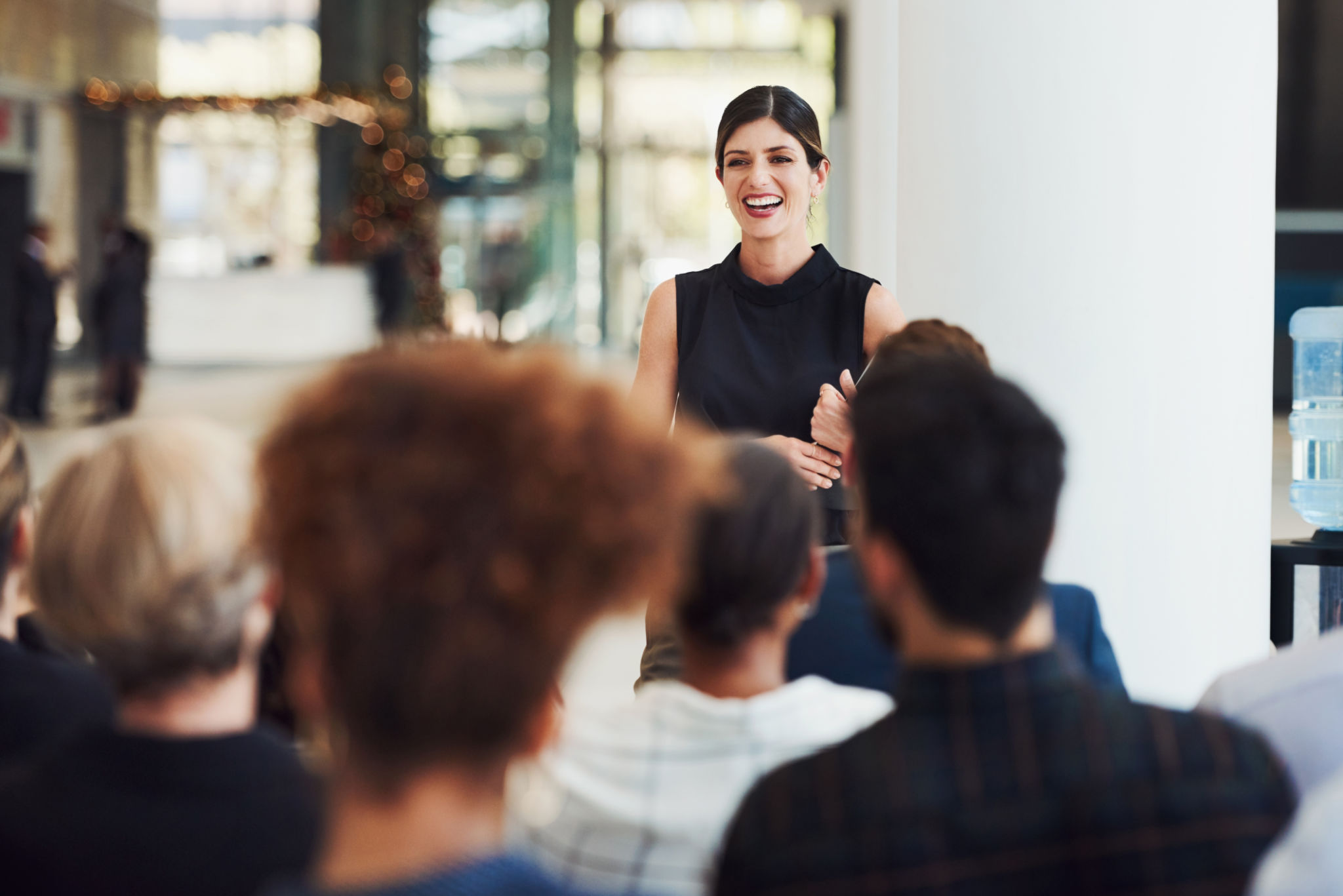
Enhancing Supplier Relationships
The quality of raw materials or components used in production directly affects the final product's quality. Building strong relationships with suppliers can help ensure consistent quality inputs. Engage in open communication with suppliers about your quality expectations and collaborate on improvement initiatives.
Conducting regular supplier audits is another effective strategy to maintain high standards. By assessing their processes and systems, you can identify areas for improvement and work together towards mutual quality goals.
The Role of Supplier Audits
Supplier audits provide valuable insights into the supply chain's quality management practices. These audits can reveal potential risks and help businesses develop contingency plans to mitigate them. By fostering partnerships based on trust and transparency, companies can achieve a more reliable supply chain.

Leveraging Customer Feedback
Customer feedback is a powerful tool for improving QC operations. Gathering insights from customers helps businesses understand their experiences and identify areas that need enhancement. Regularly reviewing feedback allows companies to make data-driven decisions to refine their products and services.
Implementing a robust feedback system can also improve customer loyalty. When customers see that their opinions matter and lead to tangible improvements, they are more likely to remain loyal to the brand.